What is the RPW method of line balancing?
We use the RPW method to analyze the processing time for each task in your production line. This is the time it takes to complete a specific task. Once we know that, we can calculate a few other key metrics:
Balance Delay: This tells us how much idle time there is in each workstation. We want to minimize this!
Smoothness Index: This measures how evenly the workload is distributed across your workstations.
Largest Track Efficiency: This tells us the efficiency of the most heavily loaded workstation.
Station Efficiency: This shows us how well each individual workstation is performing.
By crunching these numbers, the RPW method gives us a clear picture of how to balance the workload and make your production line run like a well-oiled machine.
Here’s the breakdown of how it works:
1. Rank the tasks: We start by ranking all the tasks in your production line based on their processing time. The task with the longest processing time gets the highest rank.
2. Calculate the positional weights: The positional weight for each task is determined by its rank. The higher the rank, the higher the positional weight.
3. Determine the RPW: Multiply the processing time of each task by its positional weight. The sum of these products is the RPW.
4. Balance the line: The RPW helps us to identify tasks that are taking the longest and to allocate them to workstations that have the most available time.
By using this method, you can:
Reduce idle time: By balancing the workload, you can minimize the time your workstations are sitting idle, leading to increased productivity.
Improve efficiency: A well-balanced line means tasks are completed quickly and smoothly, boosting overall efficiency.
Minimize bottlenecks: The RPW method helps us identify bottlenecks in the production process, allowing us to address them proactively.
So, if you’re looking to optimize your production line and get the most out of your resources, the RPW method is a valuable tool to consider! It’s a straightforward way to analyze your workflow and make adjustments for a more efficient and productive process.
What is the largest candidate rule technique for line balancing?
The LCR is a simple yet powerful technique that can be very effective in achieving a balanced production line. When you’re dealing with multiple work elements that have varying operating times, it’s crucial to find a method that can efficiently distribute these elements across your workstations. That’s where the LCR comes in. The main principle of the LCR is to assign the task that takes the longest amount of time first. By doing this, you ensure that no workstation is left idle while waiting for a longer task to be completed. This approach leads to a smoother production flow and reduces overall cycle time, which ultimately translates to higher efficiency and productivity.
Here’s a simple illustration to understand the LCR better: Let’s say you have four work elements with the following operating times:
Element A: 10 minutes
Element B: 5 minutes
Element C: 8 minutes
Element D: 2 minutes
Using the LCR method, you would first assign Element A (the longest operating time) to the first workstation. Then, you would assign Element C to the second workstation, followed by Element B, and finally Element D to the last workstation. This sequence ensures that the tasks are distributed in a way that optimizes the utilization of each workstation, minimizing idle time and maximizing efficiency.
As you can see, the LCR is a straightforward yet effective way to balance production lines and optimize efficiency. The focus on prioritizing the longest operating time elements makes it a valuable tool in achieving smooth workflow and minimizing bottlenecks in your production process.
What is the Kilbridge and Wester method?
Let’s dive into how this method works. Imagine you have a production line where each station needs to complete a set of tasks. The Kilbridge and Wester method helps you determine the optimal number of tasks to assign to each station to minimize the amount of time workers spend waiting around.
This method focuses on grouping tasks that have a precedence relationship—meaning, one task must be completed before the next one can start. This makes the assignment process smoother and avoids unnecessary delays.
For example, if Task A needs to be completed before Task B can begin, the Kilbridge and Wester method would place both of these tasks at the same station. This ensures that Task B doesn’t sit idle waiting for Task A to be completed at a different station.
The method relies on a “precedence matrix”, a table that shows the dependencies between tasks. The matrix clearly indicates which tasks must be completed before others, allowing you to group related tasks together efficiently.
While the Kilbridge and Wester method might not always achieve the absolute best line balancing solution, it’s a good starting point. It’s easy to understand and implement, and it can quickly bring significant improvements to your production process.
What are the rules for line balancing?
To achieve a balanced line, we must analyze and adjust the work distribution across each workstation. This involves identifying and addressing areas where the work takes longer than the takt time (bottlenecks) and areas with idle time (excess capacity). Line balancing is about optimizing the flow of work, ensuring that each workstation contributes equally to the overall production process, without creating delays or leaving resources underutilized.
Let’s delve deeper into the concept of line balancing, focusing on its rules and applications:
Rule 1: Equal Workload Distribution: Each workstation should receive an equal amount of work within the takt time. This minimizes delays and ensures that no single station becomes overloaded.
Rule 2: Minimizing Idle Time: Every station should be actively engaged in production activities. Minimizing idle time maximizes resource utilization and improves overall productivity.
Rule 3: Flexibility and Adaptability: The line balancing process should be flexible and adaptable to changes in production requirements or product variations.
Rule 4: Prioritizing Bottlenecks: Addressing bottlenecks should be a priority. These are the stations with the longest processing times, hindering the overall production rate.
Rule 5: Analyzing Task Sequences: Re-evaluating the sequence of tasks can be crucial. Sometimes, adjusting the order of tasks can reduce cycle times and create a more efficient workflow.
In essence, line balancing is a dynamic process that requires careful analysis and adjustments to achieve optimal workflow and productivity. By applying these rules, we can strive for a smoother production process, minimizing bottlenecks and maximizing resource utilization.
What is the line balancing formula?
To calculate the LBR, you take the total time for all the tasks and divide it by the number of workstations. Then, you multiply that result by the cycle time.
Let’s break down what each of those terms means:
Total task time: This is the sum of the time required to complete each individual task on your production line.
Number of workstations: This refers to the number of distinct work stations on your production line where each operator performs their designated tasks.
Cycle time: This represents the time it takes to produce one unit of your product. It’s the rate at which your production line operates.
The LBR is a crucial measure because it directly impacts your production efficiency. A high LBR indicates a well-balanced line where operators work at a consistent pace, minimizing bottlenecks and maximizing output. Conversely, a low LBR suggests uneven workload distribution, which can lead to delays, idle time, and reduced overall productivity.
Understanding the line balance rate is essential for optimizing your production process. By analyzing this metric, you can identify areas where workload needs to be adjusted, streamline your production flow, and ultimately increase your overall efficiency.
What are line balancing methods in garment industry?
Think of it like a relay race. You want each runner to carry the baton for roughly the same amount of time. In a garment factory, each workstation is a runner, and the product being made is the baton. By balancing the workload, you make sure that each station has a similar amount of work to do, preventing bottlenecks and speeding up the whole process.
There are many different ways to achieve line balancing, and the best approach will depend on the specific needs of the garment factory. Some common methods include:
Workstation assignment: This involves assigning tasks to specific workstations based on their capabilities and available time.
Line balancing software: Specialized software can help optimize task assignments, taking into account factors like task time, precedence relationships, and workstation capacity.
Line balancing by simulation: This method uses simulations to test different line balancing scenarios and identify the most efficient configuration.
By carefully balancing the workload across the line, garment factories can significantly improve their efficiency and productivity. This leads to lower costs, faster turnaround times, and higher quality products, ultimately benefiting both the factory and the customer.
What is dynamic line balancing?
Dynamic line balancing focuses on short-term capacity differences – think hours or even minutes. This means it’s constantly adjusting to changing workloads and demands. Imagine a busy call center: during peak hours, the number of calls spikes. Dynamic line balancing helps distribute those calls evenly among agents, ensuring no one gets overloaded while others sit idle.
Static line balancing takes a more long-term view. It focuses on balancing capacity over longer periods, like weeks or months. This approach is ideal when you have a consistent workload with minimal fluctuations. For example, a factory producing widgets might use static line balancing to ensure each production station has the right amount of work to handle over a typical month.
Dynamic line balancing offers several advantages:
Increased Efficiency: By distributing work based on real-time needs, it ensures optimal utilization of resources.
Reduced Bottlenecks: It prevents bottlenecks by dynamically adjusting workloads, leading to smoother workflows.
Improved Customer Service: For service-oriented businesses, dynamic line balancing helps reduce wait times and improve customer satisfaction.
To understand dynamic line balancing in practice, let’s consider an example. Think of a pizza delivery company. During rush hour, orders flood in, overwhelming the delivery drivers. Dynamic line balancing would ensure that drivers are assigned routes based on their current location and the urgency of each order. This means drivers closest to a customer needing their pizza quickly will be dispatched first, while others might be assigned orders in less-busy areas.
The constant adjustment of workloads, based on real-time factors, is what makes dynamic line balancing so effective. It’s a flexible approach that adapts to changing demands, ensuring resources are used efficiently and customer service remains high.
What is mixed model line balancing?
Mixed model line balancing is all about figuring out how to best organize tasks for different types of products, like cars, on a single assembly line. It’s like a puzzle, where you have to fit together tasks from different car models while keeping the line flowing smoothly and efficiently.
Here’s the breakdown:
Tasks: Each car model has a set of tasks, like adding the engine, putting on the wheels, or installing the dashboard.
Workstations: You have different workstations along the line, each with its own set of tools and equipment.
Processing Time: Each task takes a certain amount of time to complete.
Precedence Relationships: Some tasks have to be done before others. For example, you can’t install the wheels before adding the engine.
The goal of mixed model line balancing is to assign tasks to workstations in a way that minimizes the total time it takes to build a car, while also making sure that the line is balanced so no station is overloaded and everyone’s working efficiently.
This is done by considering the processing times and precedence relationships of each task. For example, you might decide to assign tasks that require similar tools or equipment to the same workstation. This helps to optimize the line’s efficiency by minimizing the amount of time workers spend moving between stations.
Mixed model line balancing is a complex process, but it can lead to significant improvements in productivity and efficiency. It’s a popular approach in manufacturing and is used in many industries, including automotive, electronics, and food processing.
See more here: What Are The 5 Steps For Line Balancing? | Kilbridge And Wester Method Of Line Balancing
What is Kilbridge and Wester method?
You see, the largest candidate rule can sometimes miss the mark, leading to an unbalanced workflow. The Kilbridge and Wester method comes in and offers a better way to balance the workload by taking into account the order in which tasks need to be completed. This results in a much smoother and more efficient production process.
Imagine you’re building a car. You can’t put on the wheels until the car’s chassis is built, right? The Kilbridge and Wester method helps you understand the natural order of things and makes sure that each step is done at the right time. This method is a great tool for planning out the steps in any process, whether it’s building cars, writing a book, or even just planning your day.
This method uses three simple heuristics, or rules of thumb, that are super effective at achieving a balanced workflow. The three heuristics are:
1. Assign the task with the most immediate predecessors to the workstation with the most idle time. This means that the task with the most dependencies (things that need to be done before it) goes to the station that has the most free time.
2. Assign the task with the largest number of immediate successors to the workstation with the least idle time. This means the task with the most things that need to be done after it goes to the station with the least free time.
3. Assign the task with the largest number of predecessors and successors to the workstation with the largest amount of idle time. This means the task with the most dependencies and subsequent tasks goes to the station with the most free time.
These three rules work together to create a balanced workflow where each station has a good amount of work to do and no one station is overloaded. The Kilbridge and Wester method is a simple, yet powerful tool for optimizing any process where tasks need to be completed in a specific order. It’s a great way to get the most out of your resources and make sure everything runs smoothly.
What is Kilbridge and Wester heuristic?
How does the Kilbridge and Wester heuristic work?
The priority diagram is a visual representation of the relationships between tasks. It’s like a map that shows how tasks are connected and the order in which they should be performed. The heuristic uses this diagram to identify the precedence relationships between tasks. This means it determines which tasks must be completed before others. The heuristic then assigns tasks to workstations based on these precedence relationships.
For example, imagine you’re building a car. The priority diagram might show that the engine needs to be installed before the wheels. The Kilbridge and Wester heuristic would recognize this relationship and assign the engine installation task to a workstation before the wheel installation task.
Why is the Kilbridge and Wester heuristic so useful?
It provides a straightforward and efficient way to balance assembly lines. It helps to minimize the total idle time at each workstation, ensuring that the line operates smoothly and efficiently. The heuristic is also relatively easy to understand and implement, making it a practical choice for real-world applications.
What is Kilbridge & Wester column (KWC)?
Let’s break down how the KWC works:
The Setup: The KWC starts by organizing your tasks in a specific way. Each task is represented by a row, and the columns represent the workstations on your assembly line.
The Process: You then place a “1” in the cells corresponding to the workstations where a task can be performed.
Finding the Balance: The KWC helps you visually identify the best way to allocate tasks to each workstation. This ensures that the workload is balanced and that the line operates smoothly.
Think of the KWC as a visual roadmap for line balancing. It helps you visualize the flow of work and identify potential bottlenecks before they occur.
In the automotive example you mentioned, the KWC could be applied to balance the assembly line for air conditioning duct assembly. This means you would analyze the various tasks involved in assembling the duct, such as:
* Cutting and bending the metal
* Installing the filters
* Connecting the duct to the car’s ventilation system
By using the KWC, you could determine the optimal allocation of these tasks to the workstations to ensure a smooth and efficient assembly process.
How to solve assembly line balancing problem?
Let’s break down what this means and why it’s important:
Assembly line balancing is all about finding the best way to distribute tasks among workstations on an assembly line. Think of it like a puzzle where you want to make sure each station has just the right amount of work to do without anyone getting overwhelmed or waiting around for too long.
The Rank positional weight method helps us prioritize tasks based on how long they take and how many other tasks depend on them. It’s like making a to-do list, but for assembly lines.
The Kilbridge and Wester heuristics are a set of rules that help us arrange workstations and tasks in a way that minimizes idle time and maximizes efficiency. They act as a guide for creating a smooth and efficient workflow.
By applying these methods, we were able to optimize the assembly line’s performance, leading to faster production times and reduced costs.
See more new information: countrymusicstop.com
Kilbridge And Wester Method: A Guide To Line Balancing
Hey there, ever found yourself staring at a production line, wondering how to make it more efficient? You’re not alone! That’s where line balancing comes in. It’s like a puzzle, trying to find the best way to distribute tasks across workstations to make everything run smoothly. One of the classic methods for doing this is the Kilbridge and Wester method.
Let’s dive into how it works, shall we?
Understanding the Kilbridge and Wester Method
Imagine you’re making a car. You have different operations, like putting on the wheels, adding the engine, painting the body, and so on. Each operation takes a certain amount of time. The Kilbridge and Wester method is all about figuring out the best way to assign these operations to different workstations.
It’s pretty straightforward:
1. Identify the Operations: Start by listing out all the individual tasks or operations involved in your production process. Think of it like a recipe for your product.
2. Determine the Precedence Relationships: Now, you need to figure out which operations must happen before others. This is crucial, just like you can’t bake a cake before mixing the batter. This creates a flowchart showing the order of operations.
3. Calculate the Task Times: For each operation, figure out how long it takes to complete. This can vary based on factors like worker skill or the complexity of the task.
4. Construct the Task Time Matrix: This is where the magic happens! You create a table where rows represent workstations and columns represent tasks. Each cell shows the time it takes for a task at a specific workstation.
5. Balance the Line: The goal is to create a balanced production line where the total work time at each workstation is as close as possible.
The Power of the Kilbridge and Wester Method
Why is this method so awesome? Here are a few reasons:
Simplicity: It’s relatively easy to understand and implement. No need for complicated formulas or fancy software.
Effectiveness: It helps you find a balanced line, ensuring that workstations aren’t overloaded or idle, leading to more efficient production.
Versatility: It can be used for different types of production lines, whether you’re making cars or assembling electronics.
Putting It into Practice: A Simple Example
Let’s imagine a small bakery making cupcakes. Here’s how the Kilbridge and Wester method might work:
Operations:
1. Mixing the batter: 5 minutes
2. Filling cupcake liners: 2 minutes
3. Baking: 15 minutes
4. Frosting: 3 minutes
5. Decorating: 4 minutes
Precedence Relationships:
1. You can’t fill the liners before mixing the batter, so mixing comes first.
2. You can’t bake the cupcakes before filling the liners.
3. You can’t frost or decorate until the cupcakes are baked.
Task Time Matrix:
| Workstation | Mixing | Filling | Baking | Frosting | Decorating | Total Time |
|—|—|—|—|—|—|—|
| 1 | 5 | 2 | 0 | 0 | 0 | 7 |
| 2 | 0 | 0 | 15 | 3 | 4 | 22 |
Balanced Line:
* Workstation 1: Mixing and Filling (7 minutes)
* Workstation 2: Baking, Frosting, and Decorating (22 minutes)
In this example, Workstation 2 has a longer cycle time, but the overall process is balanced.
Beyond the Basics: Addressing Limitations
The Kilbridge and Wester method is fantastic for simple production lines, but it does have some limitations. It might not be the best fit for:
Complex Precedence Relationships: When you have a lot of intricate dependencies between tasks, it can become tricky.
Multiple Products: If you’re making different products on the same line, it can be challenging to optimize for all of them.
Variable Task Times: If the time taken for a task varies significantly, the method might not be as effective.
Looking Ahead: Alternatives and Enhancements
Don’t worry, if you’re dealing with more complex situations, there are other line balancing methods available, like:
Longest Operation Time: This method focuses on assigning the longest task to a workstation to maximize utilization.
Ranked Positional Weights: This approach considers the order of operations and assigns tasks based on their weight or priority.
Computerized Methods: Software tools can handle complex line balancing problems and offer more sophisticated solutions.
You can even enhance the Kilbridge and Wester method by using techniques like:
Work Sharing: Dividing tasks between multiple workers to reduce cycle time.
Parallel Processing: Completing certain tasks simultaneously to speed up the process.
Line Balancing Software: There are software tools available that can help automate the Kilbridge and Wester method and handle more complex scenarios.
FAQs about the Kilbridge and Wester Method
Q: Can the Kilbridge and Wester method be applied to service industries?
A: Absolutely! While it originated in manufacturing, it can be applied to services as well. Think about a call center, a restaurant, or a healthcare facility. You can map out the different steps involved in providing the service and use the Kilbridge and Wester method to optimize the flow.
Q: Is the Kilbridge and Wester method only for optimizing production lines?
A: It’s primarily known for line balancing, but you can adapt it to optimize other workflows. For example, you can apply it to tasks like project management, software development, or even your daily routine.
Q: What are some real-world examples of companies using the Kilbridge and Wester method?
A: Many companies use the method or variations of it. Examples include:
Automotive manufacturers: Balancing assembly lines for cars and trucks.
Electronics manufacturers: Optimizing the production of smartphones, computers, and other devices.
Food processing companies: Streamlining packaging lines for various products.
Q: What are some common challenges when implementing the Kilbridge and Wester method?
A: Some common challenges include:
Accurate Task Time Estimation: Making sure your task times are realistic and accurate is crucial.
Precedent Relationships: Complex relationships between tasks can make the process more challenging.
Worker Variability: Workers may have different skill levels, which can affect task times.
Q: How can I learn more about the Kilbridge and Wester method?
A: There are plenty of resources available! You can find books, articles, and online tutorials that explain the method in detail.
I hope this article has given you a solid understanding of the Kilbridge and Wester method. It’s a powerful tool for improving efficiency and productivity, and it’s worth considering for your own production processes. Remember, continuous improvement is key!
Kilbridge and Wester Method | Manual Assembly Line Balancing …
#Kilbridge_Wester_Method#Line_Balancing#Facility_Planning#manual_Assembly_Line#Industrial_AutomationThis technique has received a good deal of attention in t… YouTube
Solution of the assembly line balancing problem using the rank …
In this study, the assembly line balancing problem has been solved using the Rank positional weight method, which is among the most frequently used heuristics in ScienceDirect
(PDF) A CASE STUDY OF LINE BALANCING USING
The prime objective of line balancing is to distribute tasks evenly over the workstations to minimize the idle time. In this study, ResearchGate
(PDF) Line Balancing Techniques for Productivity
The aim of this article is focusing on increasing the accuracy of standard time by time study and rearranging the work arrangement ResearchGate
Mixed Assembly Line Balancing: Theoretical background | Saylor
Theoretical background. Assembly lines. An AL consists of a production arrangement formed by workstations typically distributed over a movement system. The product is Saylor Academy
A comparative evaluation of assembly line balancing Heuristics
A comparative evaluation is presented of six popular assembly line balancing heuristics, namely, ranked positional weight, Kilbridge and Wester, Moodie Springer
(PDF) Application of Line Balancing Heuristics for
For accomplishing the purpose, different line balancing methods named Largest Candidate Rule, Kilbridge & Wester method, and Ranked Positional Weight method carried out for analyzing the line… ResearchGate
A Review of Analytical Systems of Line Balancing – JSTOR
* For a more detailed discussion of balance delay and balancing restrictions see M. KILBRIDGE and L. WESTER, “The Balance Delay Problem,” Management Sci. JSTOR
Assembly Line Balancing using Heuristic Approaches in … – CORE
simulated the line balancing to evaluate the lines performance. Literally this paper is focused on presenting three different heuristic methods: Largest Candidate Rule (LCR), CORE
Simulation for Balancing of Assembly Line using Heuristics: A
The assembly line is optimized by using the Kilbridge and Wester Column approach. To test and verify the results, the present and proposed models are simulated using arena IEEE Xplore
Kilbridge Wester Method 2 Line Balacing
Kilbridge And Wester Method | Manual Assembly Line Balancing | Industrial Automation
Using Kilbridge And Wester Method For Line Balancing
Kilbridge Wester Method 1 Line Balcning
Kilbridge And Wester Method Part 2
Link to this article: kilbridge and wester method of line balancing.
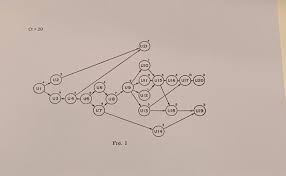
See more articles in the same category here: blog https://countrymusicstop.com/wiki