Let’s discuss the question: how are basketball players so tall. We summarize all relevant answers in section Q&A of website Countrymusicstop in category: Technology. See more related questions in the comments below.
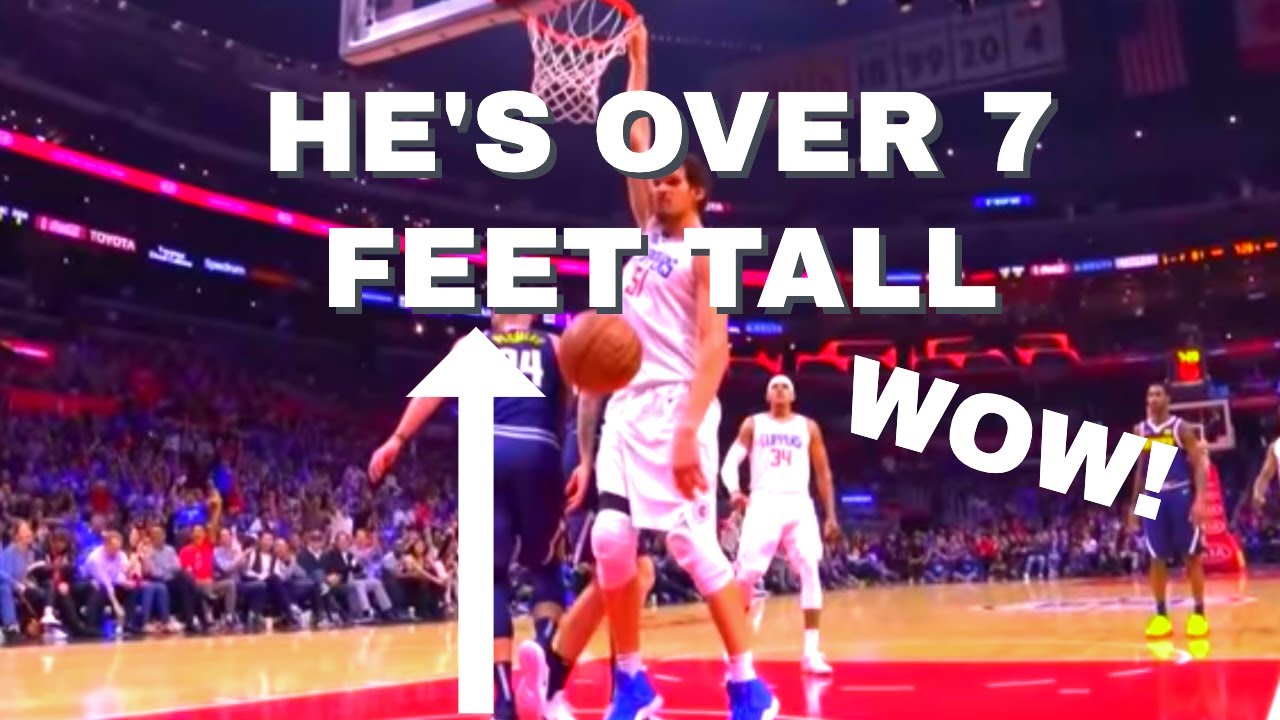
Table of Contents
How do you calculate overstocking costs?
Stockout cost formula: Number of Days Out of Stock x Average Units Sold Per Day x Price or Profit Per Unit) + Cost of Consequences = Stockout Cost. Cost of Inventory On Hand x Excess Inventory = Annual Overstock Waste Expense. Total Returns / Gross Sales = Real Return Rate. 24 thg 10, 2018
What is Understocking cost accounting?
Simply put, understocking is when your supply of a particular product fails to meet consumer demand. That is, if a customer walks into your store, asks for a product, then finds that you’ve run out. They’ll leave dissatisfied and frustrated. If it happens often enough, they might not return. 19 thg 2, 2018
What is CSL formula?
c – s. Cost of understocking Cu = p – c. Optimal cycle service level CSL* = (p – c)/(p – s) also Cu/(Cu + Co)
What is stockout cost?
A stockout is when inventory becomes unavailable, preventing an item from being purchased or shipped, resulting in a loss in sales. Stockout costs include the loss of income and customers due to a shortage of inventory from a stockout. 6 thg 5, 2020
What is EOQ and its formula?
Also referred to as ‘optimum lot size,’ the economic order quantity, or EOQ, is a calculation designed to find the optimal order quantity for businesses to minimize logistics costs, warehousing space, stockouts, and overstock costs. The formula is: EOQ = square root of: [2(setup costs)(demand rate)] / holding costs. 26 thg 2, 2020
What is CSL inventory?
Customer service level (CSL) is the most important driver of the inventory systems. It is considered as a target of the business model. Actually, it is a result of the business model. 28 thg 3, 2018
What is Understocking and overstocking?
Regardless of the terminology you employ, overstocking refers to a company over-ordering inventory and having too much stock. In contrast, understocking is when a company does not have enough inventory to keep up with the demand. 1 thg 11, 2019
What does Understocking mean?
Definition of understocking 1 archaic : a stocking for the lower leg. 2 : a stocking worn for support or warmth under another stocking.
What is Understocking at Walmart?
Smith said the workers were fired for “understocking,” or buying merchandise before it reaches store shelves. The toy, based on Sesame Street’s Elmo character, giggles and shakes when its stomach is touched. The company said it didn’t know of similar incidents at other Wal-Mart stores. 24 thg 12, 1996
How do you calculate fill rate?
Fill Rate Formula and Fill Rate Calculation Using the fill rate formula is easy. First, take the number of orders completely fulfilled and divide it by the total number of orders received. Second, multiply that number by 100. The resulting number is your fill rate percentage.
How do you calculate safety stock?
To calculate safety stock, work out your average daily use for a product and multiply it by its average lead time – how long it takes, in days, to arrive once you place an order. Then subtract this number from your maximum daily use times your maximum lead time. The result is the safety stock number for that product. 27 thg 11, 2020
What are fill rates?
Fill rate refers to the percentage of customer demand that is met by immediate stock availability, without backorders, stockouts or lost sales. Simply put, it’s an indication of how well you’re able to meet customer demand at any given time. 15 thg 12, 2017
What stockout means?
A stockout occurs when customer orders for a product exceed the amount of inventory kept on hand. This situation arises when demand is higher than expected and the amount of normal inventory and safety stock is too low to fill all orders. 16 thg 6, 2018
What are the three categories of stockout costs?
Ordering, holding, and shortage costs make up the three main categories of inventory-related costs. 23 thg 9, 2015
What is stockout production?
One of the worst things that can happen to a business is to have a stockout. This means that with no inventory of a certain item, production has to be stopped or a customer order will not be fulfilled. 5 thg 12, 2019
What is average inventory formula?
The average inventory formula is: Average inventory = (Beginning inventory + Ending inventory) / 2. However there’s more to it than simply knowing the formula. Calculating average inventory is an important part of your overall inventory strategy. 10 thg 12, 2020
How do you calculate current service level?
FAQs The most common formula used by the call center industry to calculate Service Level is: Number of calls answered within time period/ total number of call answered X 100% This is based on the objective of X% of calls answered with Y seconds.
How do you calculate cycle service level?
Cycle service level formula Add up the items sold and those not supplied (4,100 + 300 = 4,400). Divide the units sold by the result obtained in Step 1 (4,100 / 4,400 = 0.93). Multiply that number by 100 (0.93 x 100 = 93). Based on this formula, the cycle service level of that shoe is 93%. 6 thg 1, 2021
Which method is used to avoid overstocking and Understocking while production?
To minimize the likelihood of overstocking and understocking, retailers utilize a systematic process of sourcing, storing, and selling inventory, known as inventory management. 27 thg 4, 2020
What is the issue occur when Understocking?
If understocking occurs, basically you will be unable to fulfill a customer’s order at the time or within specified delivery timeframes. Given your customers will no doubt expect product when it is promised, if it is not delivered on time a lot of customer dissatisfaction will occur. 24 thg 9, 2016
What are the problems of Understocking?
Understocking has the potential to create some serious problems for all kinds of businesses. These problems can range from the loss of sales and customer loyalty to the cost of expensive restocks and missing out on discounts. 26 thg 9, 2016
What happens when animals overgraze?
Overgrazing is grazing by livestock or wildlife to the point where the grass cover is depleted, leaving bare, unprotected patches of soil. As a result, water and wind cause erosion, especially on clay soils, and the growth of poisonous plants and thorny shrubs may increase. 16 thg 11, 2001
What causes overstocking?
Overstocking, also called “surplus stock,” happens when stores purchase more product than they sell. Over-ordering inventory leaves retailers with too much stock, and that excess stock is left sitting on store shelves or in the warehouse, which can hurt profitability. 3 thg 12, 2020
What are the advantages of overstocking?
Having too much inventory is better than having no inventory, as this would prevent any production. Overstocking has the benefit that it allows a business to meet any unexpected orders. But as a rule it makes financial sense for businesses to keep down the amount of stock they hold.
What is supply chain Ccfot?
CCFOT (Customer Case Fill On Time) is used to monitor and track the reliability of performance to customers and other sites. This form the basis of the service levels of delivery to customers. Some of the factors that build to the monitoring are total cases/pallets orders, total delivered and timing of the delivery. 19 thg 3, 2019
Is fill rate a KPI?
Fill rate is one of the most crucial supply chain KPIs you can use to monitor the order fill and line fill rates. It’s represented as a percentage of packages or SKUs successfully shipped on the first attempt. Fill rate KPIs help you understand the in-full performance of your supply chain. 17 thg 4, 2019
How do you calculate safety stock in Excel?
The formula of this safety stock : (maximum sale x maximum lead time) – (average sale x average lead time). Taking the previous data, this gives you a safety stock of 427.
How are stocks calculated?
Multiply the number of shares of each stock you own by its current market price to determine your investment in each stock. For example, assume you own 1,000 shares of a $50 stock and 3,000 shares of a $25 stock. Multiply 1,000 by $50 to get $50,000. Multiply 3,000 by $25 to get $75,000.
How do you calculate safety stock and reorder point in Excel?
To calculate the reorder point in Excel, set up a table as in the image above, and use the formula =SUM(F2+G2) where Column F is your Safety Stock figure and Column G is your Lead Time Demand. 3 thg 12, 2020
How is Otif rate calculated?
The supply chain industry has not settled on an exact formula for the OTIF, but in general, the formula is: The number of deliveries made on time and complete / the total number of deliveries. 12 thg 6, 2020
What is included in holding cost?
Holding costs are costs associated with storing unsold inventory. A firm’s holding costs include storage space, labor, and insurance, as well as the price of damaged or spoiled goods. Minimizing inventory costs is an important supply-chain management strategy.
What are ordering costs?
Ordering costs are the expenses incurred to create and process an order to a supplier. These costs are included in the determination of the economic order quantity for an inventory item. Examples of ordering costs are as follows: Cost to prepare a purchase requisition. 1 thg 4, 2022
What does the term overstocking mean?
overstocked; overstocking. Definition of overstock (Entry 2 of 2) 1 transitive + intransitive : to stock too much or too many of (something) : to get or have excess inventory of (a good or goods) The big, reputable department stores frequently overstock designers’ wares for Christmas, Valentine’s Day, and Mother’s Day. …
Why are stockout costs difficult?
Stock-out costs are difficult to determine because managers have a difficult time predicting customer demand, especially if there’s a high variance… See full answer below.
What are the possible outcomes of stockout?
The most obvious consequence of stockouts is lost revenue. If a customer goes to place an order and the item is out of stock, you lose the profit of that sale. Shoppers may opt for cheaper products. Or even worse, you may lose a customer forever, which means less recurring sales in the future. 8 thg 12, 2021
Which of the following is an example of ordering cost?
Examples of order costs include the costs of preparing a requisition, a purchase order, and a receiving ticket, stocking the items when they arrive, processing the supplier’s invoice, and remitting the payment to the supplier.
How could we prevent the cost of a stockout?
How to reduce stock levels and avoid stock outs. Master your lead times. … Automate tasks with inventory management software. … Calculate reorder points. … Use accurate demand forecasting. … Try vendor managed inventory. … Implement a Just in Time (JIT) inventory system. … Use consignment inventory. … Make use of safety stock.
What is cost of running out of goods?
Key Takeaways Inventory carrying cost is the total of all expenses related to storing unsold goods. The total includes intangibles like depreciation and lost opportunity cost as well as warehousing costs. A business’ inventory carrying costs will generally total about 20% to 30% of its total inventory costs.
What are lost sales costs?
Lost sales cost (LSC) is the cost of the sales lost when we are not able to satisfy customer demand. 7 thg 6, 2017
What is the formula for cost of sales?
The cost of sales is calculated as beginning inventory + purchases – ending inventory. The cost of sales does not include any general and administrative expenses. 18 thg 1, 2022
How is cost of goods sold calculated?
The cost of goods sold formula is calculated by adding purchases for the period to the beginning inventory and subtracting the ending inventory for the period. The beginning inventory for the current period is calculated as per the leftover inventory from the previous year. 13 thg 1, 2020
How do you find cost of goods sold inventory turnover?
Inventory turnover is a ratio that shows how many times inventory has sold during a specific period of time. Dividing the cost of goods sold (COGS) by the average inventory during a particular period will give you the inventory turnover ratio.
What is service level cost?
We have said above that the target service level can be defined as a trade-off between the cost of inventory and the cost of stock-outs. As a consequence, one could get an estimate of these costs and tackle the service level issue through a cost analysis.
What does a 95% service level mean?
The desired cycle service level is 95 percent; that is, the business can tolerate stockouts of this product on no more than 5 percent of the replenishment cycles, or slightly more than two per year.
What is service level in BPO?
Call center service level is defined as the percentage of calls answered within a predefined amount of time—target time threshold. It can be measured over any period of time (i.e. 30 minutes, 1 hour, 1 day or 1 week) and for each agent, team, department or the company as a whole. 8 thg 1, 2014
How do you calculate service level in a call center in Excel?
The calculation simply is (number of calls answered in Y seconds / total calls offered) * 100. (For example you have 5000 calls offered during a month and 4250 are answered within Y seconds: (4250/5000) * 100 = 85. So the desired Service Level was well met. 25 thg 11, 2017
Should some items have 100% service level?
Service levels are considered by many retailers as part of their core IP, and tightly guarded. Nevertheless, some ballpark figures should provide a good starting point: A typical service level in retail is 90%, with high priority items reaching 95%.
What is service level in procurement?
Service level days are the approximate number of business days from Org Node approval of the BearBuy requisition to the point when the Buyer finalizes the Purchase Order if the required documentation is attached to the requisition.
What does overstocking and Understocking do to the profitability of a business?
When it comes to the consequences of understocking or overstocking your stores, there is one that overshadows every other repercussion. In short, it all boils down to money. More importantly, it’s the loss of potential sales and profit. 19 thg 2, 2018
How you would solve the problem of overstocked inventory?
9 Steps to Solve Common Inventory Problems Invest in Workforce. … Determine the Problem Area. … Invest in Software. … Avoid Dead Stock or Get Rid of It. … Save Money on Storage. … Combine Multi-Warehouse Stocks. … Regular Auditing. … Improve Item Visibility with Automation. Mục khác… • 5 thg 9, 2019
How do you solve overstocking?
Consider following these five tips for reducing your risk of overstocking and implementing better stocking practices. Invest in inventory management software. … Track sales with a POS system. … Use ABC analysis. … Assess economic and market trends. … 5 Free Templates to Better Understand Your Inventory. Mục khác… • 3 thg 12, 2020
What is overstocking and Understocking?
Regardless of the terminology you employ, overstocking refers to a company over-ordering inventory and having too much stock. In contrast, understocking is when a company does not have enough inventory to keep up with the demand. 1 thg 11, 2019
What is Understocking at Walmart?
Smith said the workers were fired for “understocking,” or buying merchandise before it reaches store shelves. The toy, based on Sesame Street’s Elmo character, giggles and shakes when its stomach is touched. The company said it didn’t know of similar incidents at other Wal-Mart stores. 24 thg 12, 1996
Is it better to overstock and Understock?
There isn’t a good choice between overstock and understock. Both have a negative impact on your business. When you have an overstock problem, you are tying up capital and space. Warehousing space costs money, on top of the cost of the product. 8 thg 4, 2020
What is the minimum stock level?
Minimum Stock Level: Definition and Explanation In other words, a minimum stock level is a minimum quantity of a particular item of material that must be kept at all times. The fixing of this level acts as a safety measure. 17 thg 9, 2021
How do you fix overgrazed pasture?
Once your pasture is germinated and growing, the new plants need time to develop strong roots. Grow the pasture to flowering height, mow and bale, cutting as high as possible. Allow the pasture to regrow and then allow animals to graze. 28 thg 1, 2016
How can we solve overgrazing?
To prevent overgrazing, the following steps can be taken: Pasture forage can be supplemented with stored livestock feed. Livestock can be pulled off pasture. A percentage of pasture acres can be planted for warm- or cool-season species while perennial-species recover.
What happens to a land when it is overgrazed?
overgrazing Pressure by grazing animals, either domestic or wild, which results in the degradation of pasture, leading to exposure of the bare soil surface and ultimately erosion and even desertification of the area.
What are the risks of overstocking?
Issues caused by overstocking Raises financial costs because the investment remains in the warehouse without creating cash flow or profits. Increases logistics costs because warehouse maintenance results in wasted space and labor expenses. Mục khác… • 11 thg 12, 2018
What are some of the costs of holding too much inventory?
having too much stock equals extra expense for you as it can lead to a shortfall in your cash flow and incur excess storage costs. having too little stock equals lost income in the form of lost sales, while also undermining customer confidence in your ability to supply the products you claim to sell. 20 thg 12, 2021
Who is in charge of inventory control?
An inventory manager is in charge of inventory in a warehouse or similar facility. Inventory managers lead a team of inventory or warehouse workers to receive and record new stock as it comes in and move stock onto trucks or shelves as needed.
What means Otif?
On time in full On time in full (OTIF) is a supply chain metric that is calculated by multiplying fill rate by on time. When perfect fill rate and perfect on time are used at the order level, this perfect OTIF meets the perfect order definition.
How do you calculate fill rate?
Fill Rate Formula and Fill Rate Calculation Using the fill rate formula is easy. First, take the number of orders completely fulfilled and divide it by the total number of orders received. Second, multiply that number by 100. The resulting number is your fill rate percentage.
How do you calculate line fill?
Dividing the number of perfectly filled lines by the overall number of ordered lines, then multiplying the result by 100, will give you the percentage line fill rate. 27 thg 10, 2015
What are fill rates?
Fill rate refers to the percentage of customer demand that is met by immediate stock availability, without backorders, stockouts or lost sales. Simply put, it’s an indication of how well you’re able to meet customer demand at any given time. 15 thg 12, 2017
How is safety stock calculated?
Safety stock is calculated by multiplying maximum daily usage (which is the maximum number of units sold in a single day) with the maximum lead time (which is the longest time it has taken the vendor to deliver the stock), then subtracting the product of average daily usage (which is the average number of units sold in … 5 thg 2, 2021
How do you find the z value for a safety stock?
Safety stock = Z-score x standard deviation of lead time x average demand. For example, if aiming for a Z-score of 1.65, with average demand constant at 20 units per month, and lead times over a six month period being 2, 1.5, 2.3, 1.9, 2.1, and 2.8 months, then Safety Stock = 1.65 x . 43 x 20 = 14.3 units.
How do you calculate factor of safety?
Factor of safety=Ultimate Load (Strength)/Allowable Load (Stress) As understood from the above equation the allowable stress is always less than the ultimate failure stress. Hence, the factor of safety is always greater than 1.
How do I calculate how much shares to buy?
How many shares can you buy based on price? Find the current share price of the stock you want. … Divide the amount of money you have available to invest in the stock by its current share price. If your broker allows you to buy fractional shares, the result is the number of shares you can buy.
How is stock reorder point calculated?
The basic formula for the reorder point is to multiply the average daily usage rate for an inventory item by the lead time in days to replenish it. 19 thg 1, 2022
How do I calculate reorder in Excel?
To calculate the reorder point in Excel, set up a table as in the image above, and use the formula =SUM(F2+G2) where Column F is your Safety Stock figure and Column G is your Lead Time Demand. 3 thg 12, 2020
What is OTIF performance?
On-time in-full (OTIF) is a supply chain metric for measuring performance in the logistics industry. OTIF generally refers to a supplier’s ability to deliver product within prescribed delivery windows and at full quantities ordered.
What is Stockout rate?
The Stockout Rate was defined as the percentage of items not available upon the requested need date.
How do you calculate annual holding cost?
Using this information, you can calculate your holding costs as follows: Inventory holding sum = inventory service cost + capital cost + storage space cost + inventory risk. Inventory holding sum = $20,000. (Inventory holding sum / total value of inventory) x 100 = holding costs (%) Mục khác… • 22 thg 2, 2021
How do you calculate annual holding cost per unit?
We can now compute the annual holding cost as H*(Q/2) or $5per unit per year * 50 units = $250 per year.
What are the 3 types of ordering costs?
Ordering, holding, and shortage costs make up the three main categories of inventory-related costs. 23 thg 9, 2015
What is EOQ and its formula?
Also referred to as ‘optimum lot size,’ the economic order quantity, or EOQ, is a calculation designed to find the optimal order quantity for businesses to minimize logistics costs, warehousing space, stockouts, and overstock costs. The formula is: EOQ = square root of: [2(setup costs)(demand rate)] / holding costs. 26 thg 2, 2020
What are the possible outcomes of stockout?
The most obvious consequence of stockouts is lost revenue. If a customer goes to place an order and the item is out of stock, you lose the profit of that sale. Shoppers may opt for cheaper products. Or even worse, you may lose a customer forever, which means less recurring sales in the future. 8 thg 12, 2021
How could we prevent the cost of a stockout?
How to reduce stock levels and avoid stock outs. Master your lead times. … Automate tasks with inventory management software. … Calculate reorder points. … Use accurate demand forecasting. … Try vendor managed inventory. … Implement a Just in Time (JIT) inventory system. … Use consignment inventory. … Make use of safety stock.
Why are stockout costs difficult?
Stock-out costs are difficult to determine because managers have a difficult time predicting customer demand, especially if there’s a high variance… See full answer below.
What is total ordering cost?
Ordering costs are the expenses your company incurs to purchase and receive the products it stocks in its inventory. These ordering costs can include shipping fees, unexpected transportation costs, inspection fees and other expenses necessary to acquire inventory products. 10 thg 6, 2021
What is stockout in supply chain?
Stockouts are what happen when you run out of inventory of a particular item. An out-of-stock can happen anywhere in the supply chain, but it impacts retailers’ shelves and profits the most when it occurs as the customer is about to purchase. 8 thg 12, 2021
What is included in holding cost?
Holding costs are costs associated with storing unsold inventory. A firm’s holding costs include storage space, labor, and insurance, as well as the price of damaged or spoiled goods. Minimizing inventory costs is an important supply-chain management strategy.
What causes a stockout?
Stockouts occur when products are unavailable to customers who want to make a purchase. Stock shortages occur in both physical stores and for online retailers. Supply shortages and improper inventory management commonly cause stockouts. 1 thg 7, 2021
How do I calculate cost of goods manufactured?
The cost of goods manufactured equation is calculated by adding the total manufacturing costs; including all direct materials, direct labor, and factory overhead; to the beginning work in process inventory and subtracting the ending goods in process inventory.
What is the formula for cost of sales?
The cost of sales is calculated as beginning inventory + purchases – ending inventory. The cost of sales does not include any general and administrative expenses. 18 thg 1, 2022
What are the 3 costs included in product costs?
The three general categories of costs included in manufacturing processes are direct materials, direct labor, and overhead.
How do you calculate lost sales?
Measuring lost sales indicator Lost sales can be measured in multiple ways. The simplest – is to calculate how many days your product was absent in stock. Dividing that number by amount of days in the year you can get an approximate feeling of how many more you could have sold if the product would have been available. 18 thg 4, 2018
How do you calculate lost sales in retail?
The difference between the average demand and actual sales is your loss. For example on day 4 sales would have been 106 but you sold only 95, so lost sales equals 11 units. I hope this helps. 13 thg 4, 2020
How do you reduce the cost of lost sales?
Here are four ways to help reduce lost sales: Record Your Lost Sales. As we mentioned above, there are a number of reasons that a company can lose a sale. … Organize Your Parts. … Improve Your Forecasts. … Have Back Up Suppliers. 23 thg 7, 2018
How do I calculate cost of sales in Excel?
Cost of Sales = Beginning Inventory + Raw Material Purchase + Cost of Direct Labor + Overhead Manufacturing Cost – Ending Inventory Cost of Sales = $20,000 + $100,000 + $70,000 + $60,000 – $15,000. Cost of Sales= $235,000.
How do you calculate cost of sales in Excel?
Cost of Goods Sold = Beginning Inventory + Purchases during the year – Ending Inventory Cost of Goods Sold = Beginning Inventory + Purchases during the year – Ending Inventory. Cost of Goods Sold = $20000 + $5000 – $15000. Cost of Goods Sold = $10000.
What is cost of goods sold Example?
The cost of goods made or bought is adjusted according to change in inventory. For example, if 500 units are made or bought but inventory rises by 50 units, then the cost of 450 units is cost of goods sold. If inventory decreases by 50 units, the cost of 550 units is cost of goods sold.
Is cost of sales the same as cost of goods sold?
Companies will often list on their balance sheets cost of goods sold (COGS) or cost of sales (and sometimes both), leading to confusion about what the two terms mean. Fundamentally, there is almost no difference between cost of goods sold and cost of sales. In accounting, the two terms are often used interchangeably.
How do you calculate inventory turnover in Excel?
If you know your total cost of goods sold, and your average inventory value for the same period of time, you can calculate your inventory turnover in Excel by dividing the cost of goods sold by the average. To do this, divide the cell with the total value by the cell with the average value. For example: A1/A2. 20 thg 8, 2021
How is inventory calculated?
To calculate it, divide the total ending inventory into the annual cost of goods sold. For example: your ending inventory is $30,000 and your cost of goods sold is $45,000. Divide $45,000 by $30,000 which equals 1.5. This means your inventory has turned (been sold) one- and one-half times during the year. 13 thg 1, 2021
How do you calculate service level operations?
Cycle service level formula Add up the items sold and those not supplied (4,100 + 300 = 4,400). Divide the units sold by the result obtained in Step 1 (4,100 / 4,400 = 0.93). Multiply that number by 100 (0.93 x 100 = 93). 6 thg 1, 2021
What is CSL in supply chain?
Introduction. CSL stands for Controlled Shipping Level. Controlled Shipping is both a systematic procedure and a status. If a supplier has shipped non-conform parts, its customer has the right to put the supplier into the state of “Controlled Shipping”. 5 thg 1, 2017
What are the 3 levels of service?
According to Andrew Gibson there are three main levels of customer service. They are the expected level, the desired level, and the unanticipated level. 3 thg 3, 2009
Which demand 100 service level is feasible?
While a 100% service level might – i.e. service all customers all the time – appear desirable, it is usually not a feasible option. The cycle service level should not be confused with the fill rate which represent the fraction of demand that is served without delays or lost sales.
What z value would be appropriate for a 98% service level?
If I want to achieve a service level of 98% I just need to look-up what is the Z-factor corresponding to 98%, which is Z = 2.05. Therefore I need a safety stock equivalent to my average demand + 2.05 standard deviations, which is 100 + 2.05*50 = 202.5. 23 thg 12, 2018
Should some items have 100% service level?
Service levels are considered by many retailers as part of their core IP, and tightly guarded. Nevertheless, some ballpark figures should provide a good starting point: A typical service level in retail is 90%, with high priority items reaching 95%.
What is KPI in BPO?
A KPI (Key Performance Indicator) is a measurable value, or values, that demonstrates how effectively a company, department, team, or individual is achieving business goals. 5 thg 10, 2017
What is an SLA in call center?
A SLA is your call center’s promise of maintaining a certain standard of service to your clients and customers and, typically speaking, the SLA will specify that your call center is committed to answering a set percentage of calls within a certain number of seconds, such as answering 75% of calls within 20 seconds.
How is occupancy calculated in BPO?
The most obvious call center occupancy formula would be to divide the time an agent spends on calls by all of their available working time. For instance, if an agent spent 54 minutes on calls during one hour (aka 60 minutes) of work, they would have an occupancy rate of 90 percent (54/60 = 90%). 5 thg 7, 2016
How is call center service level calculated?
The service level formula is simply the number of calls answered within the service level threshold divided by the number of calls offered, multiplied by 100. This then gives you a percentage service level. 22 thg 11, 2017
How is call center utilization rate calculated?
Simply take the amount of time your agents are reported as being on calls or performing call-related tasks and divide it by the total time they are on the clock. Multiply the resulting number by 100, and you have the agent utilization percentage. 5 thg 12, 2018
What is Z in safety stock?
Z is the desired service level, σLT is the standard deviation of lead time, and D avg is the demand average. Don’t be intimidated. The simplest method for calculating safety stock only requires a four-step process to calculate these variables. 21 thg 9, 2020
What is the difference between service level and fill rate?
Service level is calculating the fraction of replenishment cycle that ends with all customer demand met, while fill rate is calculating the fraction of demand that is satisfied from available inventory. 11 thg 3, 2021
What is a target service level?
The target service level can be defined as a trade-off between the cost of inventory and the cost of stock-outs. As a consequence, one could get an estimate of these costs and tackle the service level issue through a cost analysis.
What is SLA and KPI?
The difference between SLAs and KPIs An SLA is an agreement between you and your customer that defines how your relationship will work in the future. Key performance indicators (KPIs) are the metrics chosen to gauge how well a team performed against agreed standards.
What is SLA and OLA?
Definition: The Service Level Agreement (SLA) is an agreement between an IT service provider and a customer. The Operational Level Agreement (OLA) is an agreement between an IT service provider and another part of the same organization, governing the delivery of a infrastructure service.
What is difference between SLA and SLO?
An SLO (service level objective) is an agreement within an SLA about a specific metric like uptime or response time. So, if the SLA is the formal agreement between you and your customer, SLOs are the individual promises you’re making to that customer.
What is Understocking and overstocking?
Regardless of the terminology you employ, overstocking refers to a company over-ordering inventory and having too much stock. In contrast, understocking is when a company does not have enough inventory to keep up with the demand. 1 thg 11, 2019
How do you solve overstocking?
Consider following these five tips for reducing your risk of overstocking and implementing better stocking practices. Invest in inventory management software. … Track sales with a POS system. … Use ABC analysis. … Assess economic and market trends. … 5 Free Templates to Better Understand Your Inventory. Mục khác… • 3 thg 12, 2020
Which method is used to avoid overstocking and Understocking while production?
To minimize the likelihood of overstocking and understocking, retailers utilize a systematic process of sourcing, storing, and selling inventory, known as inventory management. 27 thg 4, 2020
What are the problems with Understocking?
Understocking has the potential to create some serious problems for all kinds of businesses. These problems can range from the loss of sales and customer loyalty to the cost of expensive restocks and missing out on discounts. 26 thg 9, 2016
What is overstock goods?
When referring to overstock merchandise in the form of consumer goods in a retail operation, the term refers to goods that have never been purchased by a customer but that are considered excessive stock from shelves and/or warehouses.
What are the consequences of overstocking and Understocking?
When it comes to the consequences of understocking or overstocking your stores, there is one that overshadows every other repercussion. In short, it all boils down to money. More importantly, it’s the loss of potential sales and profit. 19 thg 2, 2018
Why is overstocking a problem?
Businesses need to be aware of the disadvantages of having too much inventory. Inventory can go out of fashion or spoil meaning the business will have to write it off as a loss. Having too much inventory results in higher storage costs in terms of bothoverheads and security.
What is the problem with overstocking?
Issues caused by overstocking Raises financial costs because the investment remains in the warehouse without creating cash flow or profits. Increases logistics costs because warehouse maintenance results in wasted space and labor expenses. 11 thg 12, 2018
What is Understocking at Walmart?
Smith said the workers were fired for “understocking,” or buying merchandise before it reaches store shelves. The toy, based on Sesame Street’s Elmo character, giggles and shakes when its stomach is touched. The company said it didn’t know of similar incidents at other Wal-Mart stores. 24 thg 12, 1996
What is the minimum stock level?
Minimum Stock Level: Definition and Explanation In other words, a minimum stock level is a minimum quantity of a particular item of material that must be kept at all times. The fixing of this level acts as a safety measure. 17 thg 9, 2021
How do you calculate stock level?
Average Stock Level: The Average stock level is calculated such as: Average Stock Level = Minimum stock Level + 1/2 of Reorder Quantity.
What are ordering costs?
Ordering costs are the expenses incurred to create and process an order to a supplier. These costs are included in the determination of the economic order quantity for an inventory item. Examples of ordering costs are as follows: Cost to prepare a purchase requisition. 1 thg 4, 2022
What is maximum stock level in cost accounting?
The maximum stock level is a not-to-exceed amount used for inventory planning. This stock level is based on a calculation of the cost of storage, standard order quantities, and the risk of inventory becoming obsolete or spoiling with the passage of time. 10 thg 3, 2022
How do you tell if a pasture is overgrazed?
Some common signs of overgrazing may include: Running out of feed before the grazing season ends. Seeing more ribs than ribeyes. Seeing more bare and open spaces than covered land. Water ponding on the surface due to lack of infiltration. A change in forage species. The gate or water area trampled bare. Mục khác… • 25 thg 11, 2015
How long should a pasture rest between grazing?
With experience will come the knowledge needed to determine when a pasture has recovered and is ready for grazing. As a general rule of thumb a minimum recovery period is estimated to be at least 6 weeks. 7 thg 5, 2020
How can we protect rangelands?
Benefits of Conservation Easements Rangelands are home to various plant and animal species, and conservation easements have proven to be one of the most effective tools for the permanent protection of millions of acres of natural habitats and undeveloped spaces. Conservation easements also protect resources. 24 thg 9, 2021
What is an example of overgrazing?
The Dragon’s Blood Tree used to grow all over Socotra, however its range has been significantly reduced as a result of goats’ overgrazing. The goats eat the young trees and seeds before they have a chance to fully develop and destroy the already fragile land, rendering it too weak to support new plant growth. 23 thg 7, 2020
What happens when animals overgraze?
Overgrazing is grazing by livestock or wildlife to the point where the grass cover is depleted, leaving bare, unprotected patches of soil. As a result, water and wind cause erosion, especially on clay soils, and the growth of poisonous plants and thorny shrubs may increase. 16 thg 11, 2001
How overgrazing can be controlled?
On the management front, Bishopp offers the following suggestions to avoid an overgrazing situation: Have feed on-hand or stockpiled in the spring so you are not forced to graze too early. Use a grazing chart to plan out a rotation. Monitor grass growth and rainfall. Maintain proper pasture residuals for your area. 10 thg 3, 2018
Why is overgrazing harmful?
Overgrazing can reduce ground cover, enabling erosion and compaction of the land by wind and rain.. This reduces the ability for plants to grow and water to penetrate, which harms soil microbes and results in serious erosion of the land. 2 thg 1, 2022
What are the ill effects of over grazing?
Overgrazing combined with overstocking has the most damaging outcomes to the world’s natural environment. The scarcity of water resources, water pollution, degeneration of coral reefs, and eutrophication are all connected to overgrazing. The chief polluting elements include farm chemicals and animal wastes.
How do you solve inventory rotation problems?
How to Solve Common Inventory Problems Determine the Problem Areas. … Invest in a Bigger Team. … Invest in Software. … Avoid Dead Stock. … Save Money on Storage. … Regular Auditing. … Utilize Automation. … Partner with a Third-Party Logistics Provider. Mục khác… • 21 thg 4, 2021
What are the costs of holding inventories?
Holding costs are costs associated with storing unsold inventory. A firm’s holding costs include storage space, labor, and insurance, as well as the price of damaged or spoiled goods. Minimizing inventory costs is an important supply-chain management strategy.
What are the cost of having inventory?
Key Takeaways Inventory carrying cost is the total of all expenses related to storing unsold goods. The total includes intangibles like depreciation and lost opportunity cost as well as warehousing costs. A business’ inventory carrying costs will generally total about 20% to 30% of its total inventory costs.
Why is inventory expensive?
Inventory service cost The level of inventory is the amount of inventory the company keeps on hand to fulfill its orders—a high level of inventory makes it easier to meet the customer demand. High levels of inventory attract higher insurance premiums and taxes, raising the total inventory service cost.
What are the 4 types of inventory?
There are four main types of inventory: raw materials/components, WIP, finished goods and MRO. 21 thg 12, 2021
What is inventory control?
Inventory control, also called stock control, is the process of managing a company’s inventory levels, whether that be in their own warehouse or spread over other locations. It comprises management of items from the time you have them in stock to their final destination (ideally to customers) or disposal (not ideal).
Who Should an inventory manager report to?
Merchants Traditionally, inventory planning, forecasting and management functions have reported to the Merchants.
How is OTIF calculated?
The supply chain industry has not settled on an exact formula for the OTIF, but in general, the formula is: The number of deliveries made on time and complete / the total number of deliveries. 12 thg 6, 2020
How is delivery performance calculated?
To calculate OTD rate, you divide the total number of orders delivered by the number of deliveries that arrived after the promised delivery date. Most companies measure OTD with a date range, typically spanning five days before the delivery due date. 22 thg 10, 2021
How is Walmart OTIF calculated?
How Is OTIF Calculated? OTIF is calculated on the percentage of the times deliveries hit the assigned delivery widow and the percentage of the physical freight that was accurate (see Walmart OTIF Guidelines below). Monetary penalties are also calculated on a percentage of the order. 15 thg 2, 2021
What is Stockout rate?
The Stockout Rate was defined as the percentage of items not available upon the requested need date.
What is supply chain Ccfot?
CCFOT (Customer Case Fill On Time) is used to monitor and track the reliability of performance to customers and other sites. This form the basis of the service levels of delivery to customers. Some of the factors that build to the monitoring are total cases/pallets orders, total delivered and timing of the delivery. 19 thg 3, 2019
What are fill rates?
Fill rate refers to the percentage of customer demand that is met by immediate stock availability, without backorders, stockouts or lost sales. Simply put, it’s an indication of how well you’re able to meet customer demand at any given time. 15 thg 12, 2017
What is the safety stock formula?
What is the safety stock formula? The safety stock formula is therefore: [maximum daily use x maximum lead time] – [average daily use x average lead time] = safety stock. 27 thg 11, 2020
Is fill rate a KPI?
Fill rate is one of the most crucial supply chain KPIs you can use to monitor the order fill and line fill rates. It’s represented as a percentage of packages or SKUs successfully shipped on the first attempt. Fill rate KPIs help you understand the in-full performance of your supply chain. 17 thg 4, 2019
How is supply chain fill rate calculated?
The fill rate formula is simple. You divide the number of customer orders shipped in full by the number of customer orders placed. When you multiply that number by 100, you will learn your fill rate in the form of a percentage. 28 thg 8, 2019
What is fill rate programmatic?
Fill rate is the percentage of ad requests that get filled by the ad networks you’re working with. It’s calculated by dividing the number of ad impressions an app actually serves, by the number of times an app requested an ad from a network. 8 thg 4, 2018
How do you calculate ordering cost?
Ordering cost is the cost of placing an order to the supplier for inventory. The number of orders is calculated by the annual quantity demanded divided by volume per order. … #2 – Ordering Cost D = Annual quantity demanded. Q = Volume per order. Annual Ordering Cost.
How do you calculate safety stock in Excel?
The formula of this safety stock : (maximum sale x maximum lead time) – (average sale x average lead time). Taking the previous data, this gives you a safety stock of 427.
What is inventory formula?
Average inventory formula: Take your beginning inventory for a given period of time (usually a month). Add that number to your end of period inventory (month, season, or year), and then divide by 2 (or 7, 13, etc). (Beginning of Month Inventory + End of Month Inventory) ÷ 2 = Average Inventory (Month)
What z value would be appropriate for a 98% service level?
If I want to achieve a service level of 98% I just need to look-up what is the Z-factor corresponding to 98%, which is Z = 2.05. Therefore I need a safety stock equivalent to my average demand + 2.05 standard deviations, which is 100 + 2.05*50 = 202.5. 23 thg 12, 2018
What is EOQ and its formula?
Also referred to as ‘optimum lot size,’ the economic order quantity, or EOQ, is a calculation designed to find the optimal order quantity for businesses to minimize logistics costs, warehousing space, stockouts, and overstock costs. The formula is: EOQ = square root of: [2(setup costs)(demand rate)] / holding costs. 26 thg 2, 2020
What is a 4 to 1 safety factor?
In the section covering leaf chain, the Machinery Directive states that the minimum safety factor when lifting a weight should be 4:1. In other words, the leaf chain should be able to lift four times the maximum weight it will be lifting in its working life.
What does a safety factor of 1.5 mean?
1.5 – 2. For use with ordinary materials where loading and environmental conditions are not severe. 2 – 2.5. For use with less tried and for brittle materials where loading and environmental conditions are not severe.
How much is factor of safety?
A usually applied Safety Factor is 1.5, but for pressurized fuselage it is 2.0, and for main landing gear structures it is often 1.25. In some cases it is impractical or impossible for a part to meet the “standard” design factor.
How do I calculate profit per share?
Typically profit share is calculated by determining the ratio of the employee’s compensation to the total compensation of all employees. For example, if an employee earns 1% of all compensation, then they receive 1% of the profits for the year or period. 1 thg 11, 2021
What are 100 stock shares called?
A round lot is a standard number of securities to be traded on an exchange. In stocks, a round lot is considered 100 shares or a larger number that can be evenly divided by 100. In bonds, a round lot is usually $100,000 worth.
How much does it cost to order at reorder point?
The formula for reorder quantity is the average daily usage multiplied by the average lead time. The reorder point is the reorder quantity plus the allowance for safety stock. If average daily sales of widgets is 2.5 and the average lead time is eight days, the reorder quantity equals 20 widgets.
How do you calculate stock replenishment?
Stock replenishment principles Multiply your maximum daily usage by your maximum lead time in days. Multiply your average daily usage by your average lead time in days. Calculate the difference between the two to determine your safety stock. 31 thg 5, 2019
What is reorder level in cost accounting?
In management accounting, reorder level (or reorder point) is the inventory level at which a company would place a new order or start a new manufacturing run. Reorder level depends on a company’s work-order lead time and its demand during that time and whether the company maintain a safety stock.
How do you calculate reorder period?
To calculate the reorder level, multiply the average daily usage rate by the lead time in days for an inventory item. 13 thg 5, 2017
What OTIF means?
On time in full On time in full (OTIF) is a supply chain metric that is calculated by multiplying fill rate by on time. When perfect fill rate and perfect on time are used at the order level, this perfect OTIF meets the perfect order definition.
What does OTIF stand for in manufacturing?
On-time in-full (OTIF) is a supply chain metric for measuring performance in the logistics industry. OTIF generally refers to a supplier’s ability to deliver product within prescribed delivery windows and at full quantities ordered.
What are the KPIs for supply chain?
Top 10 Supply Chain Management KPIs #1. Cash to Cash Cycle Time. … #2. Perfect Order Rate. … #3. Fill Rate. … #4. Customer Order Cycle Time. … #5. Inventory Days of Supply. … #6. Inventory Turnover. … #7. Reasons for Return. … #8. On-Time Delivery. Mục khác… • 4 thg 10, 2021
What is stockout production?
One of the worst things that can happen to a business is to have a stockout. This means that with no inventory of a certain item, production has to be stopped or a customer order will not be fulfilled. 5 thg 12, 2019
How could we prevent the cost of a stockout?
How to reduce stock levels and avoid stock outs. Master your lead times. … Automate tasks with inventory management software. … Calculate reorder points. … Use accurate demand forecasting. … Try vendor managed inventory. … Implement a Just in Time (JIT) inventory system. … Use consignment inventory. … Make use of safety stock.
What is a stockout in business?
Stockouts are what happen when you run out of inventory of a particular item. An out-of-stock can happen anywhere in the supply chain, but it impacts retailers’ shelves and profits the most when it occurs as the customer is about to purchase. 8 thg 12, 2021
How is total cost calculated?
The formula for calculating average total cost is: (Total fixed costs + total variable costs) / number of units produced = average total cost. (Total fixed costs + total variable costs) New cost – old cost = change in cost. New quantity – old quantity = change in quantity. Mục khác… • 22 thg 2, 2021
What is annual holding cost?
Annual holding cost = average inventory level x holding cost per unit per year = order quantity/2 x holding cost per unit per year. 2. Setup or ordering costs: cost involved in placing an order or setting up the equipment to make the product.
How do you calculate holding costs in real estate?
While these costs will vary greatly from house to house, experienced house flippers take a simple educated estimate of 1.5% of the final house sale price or the estimated sale price. Example: If the house will be sold for $220,000, then 1.5% will be $3,300. In this example, $3,300 will be your holding costs.
What are examples of ordering costs?
Examples of order costs include the costs of preparing a requisition, a purchase order, and a receiving ticket, stocking the items when they arrive, processing the supplier’s invoice, and remitting the payment to the supplier.
What is total ordering cost?
Ordering costs are the expenses your company incurs to purchase and receive the products it stocks in its inventory. These ordering costs can include shipping fees, unexpected transportation costs, inspection fees and other expenses necessary to acquire inventory products. 10 thg 6, 2021
What is meant by ordering cost?
Ordering costs are the expenses incurred to create and process an order to a supplier. These costs are included in the determination of the economic order quantity for an inventory item. Examples of ordering costs are as follows: Cost to prepare a purchase requisition. 15 thg 1, 2021
What are the three categories of stockout costs?
Ordering, holding, and shortage costs make up the three main categories of inventory-related costs. 23 thg 9, 2015
Why are stockout costs difficult?
Stock-out costs are difficult to determine because managers have a difficult time predicting customer demand, especially if there’s a high variance… See full answer below.
What is shortage cost?
When demand exceeds the available inventory for an item, the demand and customer goodwill may be lost. The associate cost is called shortage cost. Some writers estimate shortage costs as equal to the product’s contribution margin.
What are the possible outcomes of stockout?
The most obvious consequence of stockouts is lost revenue. If a customer goes to place an order and the item is out of stock, you lose the profit of that sale. Shoppers may opt for cheaper products. Or even worse, you may lose a customer forever, which means less recurring sales in the future. 8 thg 12, 2021
What is included in holding cost?
Holding costs are costs associated with storing unsold inventory. A firm’s holding costs include storage space, labor, and insurance, as well as the price of damaged or spoiled goods. Minimizing inventory costs is an important supply-chain management strategy.
What causes a stockout?
Stockouts occur when products are unavailable to customers who want to make a purchase. Stock shortages occur in both physical stores and for online retailers. Supply shortages and improper inventory management commonly cause stockouts. 1 thg 7, 2021
How do you reduce stock out cost in Capsim?
How do you get rid of inventory in Capsim? In the production screen, sell all of the available capacity. Remember that when you liquidate, you must sell all but one unit of capacity in order for the simulation to sell off all inventory at 100 percent of the price.
What are the possible consequences for a firm if its customer experiences a stockout?
Negative Effects of OOS Suppliers Retailers Distorted perception of store demand Increased operational costs (providing “rain checks”, unplanned restocking or looking for stock in back room) Direct sales loss Decreased store loyalty Damaged brand reputation/brand loyalty Increased likelihood for shopping at competitor stores 2 hàng khác
What are the two types of costs associated with inventory?
There are two types of costs associated with inventory: creation/acquisition costs and carrying costs. 4 thg 1, 2022
How do you calculate order in Excel?
Economic Order Quantity is Calculated as: Economic Order Quantity = √(2SD/H)
How do you calculate orders?
Order Quantity Formula To calculate the optimum order quantity “Q,” take the square root of the following: “2N” multiplied by “P” and divided by “H.” “N” is the number of units sold per year, “P” is the cost to place one order and “H” is the cost of holding one unit of inventory for one year. 26 thg 9, 2017
What is stockout rate?
The Stockout Rate was defined as the percentage of items not available upon the requested need date.
What are fill rates?
The definition of fill rate is the percentage of customer orders you’re able to meet without running out of stock at any given time. A strong fill rate is at or near 100%, meaning you’re able to fulfill all of the wholesale sales you make without stockouts, backorders, or lost sales.
How do you calculate annual holding cost?
Using this information, you can calculate your holding costs as follows: Inventory holding sum = inventory service cost + capital cost + storage space cost + inventory risk. Inventory holding sum = $20,000. (Inventory holding sum / total value of inventory) x 100 = holding costs (%) Mục khác… • 22 thg 2, 2021
How do you calculate annual holding cost per unit?
We can now compute the annual holding cost as H*(Q/2) or $5per unit per year * 50 units = $250 per year.
How do you calculate holding cost in EOQ?
EOQ formula Determine the demand in units. Determine the order cost (incremental cost to process and order) Determine the holding cost (incremental cost to hold one unit in inventory) Multiply the demand by 2, then multiply the result by the order cost. Divide the result by the holding cost. Mục khác… • 13 thg 11, 2019
Why is safety stock needed?
Safety stock protects you against the sudden demand surges and inaccurate market forecasts that can happen during a busy or festive season. It serves as a cushion when the products you’ve ordered take longer to reach your warehouse than you expected. 5 thg 2, 2021
How do you find cost of goods manufactured and cost of goods sold?
The calculation of the cost of goods sold for a manufacturing company is: Beginning Inventory of Finished Goods. Add: Cost of Goods Manufactured. Equals: Finished Goods Available for Sale. Subtract: Ending Inventory of Finished Goods. Equals: Cost of Goods Sold.
What is total manufacturing cost?
Total manufacturing costs showcase how much your company spent to produce its inventory in a given period of time. This includes a thorough account of the cost of overhead, materials used, labor, and any other manufacturing expenses that contributed to completing the product. 1 thg 7, 2021
How do I calculate cost of sales in Excel?
Cost of Sales = Beginning Inventory + Raw Material Purchase + Cost of Direct Labor + Overhead Manufacturing Cost – Ending Inventory Cost of Sales = $20,000 + $100,000 + $70,000 + $60,000 – $15,000. Cost of Sales= $235,000.
How do you calculate cost of sales in Excel?
Cost of Goods Sold = Beginning Inventory + Purchases during the year – Ending Inventory Cost of Goods Sold = Beginning Inventory + Purchases during the year – Ending Inventory. Cost of Goods Sold = $20000 + $5000 – $15000. Cost of Goods Sold = $10000.
How do you calculate cost of goods sold from sales?
At a basic level, the cost of goods sold formula is: Starting inventory + purchases − ending inventory = cost of goods sold.
How do I calculate product cost?
How to calculate product cost Categorize manufacturing costs for a specific product. … Tally the costs of all the direct materials used to make the product. … Add up all the costs for direct labor. … Find the sum of the manufacturing overhead costs. … Count the total number of new units. Mục khác… • 23 thg 2, 2021
How do I calculate cost of goods manufactured?
The cost of goods manufactured equation is calculated by adding the total manufacturing costs; including all direct materials, direct labor, and factory overhead; to the beginning work in process inventory and subtracting the ending goods in process inventory.
What is the cost of a product?
Product costs are the direct costs involved in producing a product. A manufacturer, for example, would have product costs that include: Direct labor. Raw materials.
What is the cost of a lost sale?
Lost sales cost (LSC) is the cost of the sales lost when we are not able to satisfy customer demand. 7 thg 6, 2017
How is Stockout calculated?
How to calculate safety stock Find the following for each SKU: Maximum daily usage. … Calculate your max (maximum daily usage x maximum lead time) Next you’ll multiply the maximum daily usage by the maximum lead time. … Calculate your average (average daily usage x average lead time) … Subtract the two. 12 thg 7, 2019
What is a lost sale in inventory?
By definition, a lost sale is a selling opportunity you miss out on for items that are out-of-stock. You can’t sell something that isn’t in your inventory. That is why it is essential to analyze your lost sales, learn from your past mistakes and replenish your stock to meet future demand. 6 thg 12, 2018
How do you avoid losing sales?
Here are five ways to improve the way you keep track of your inventory, and prevent out-of-stock scenarios: Ensure your data is reliable and up to date. … Anticipate demand with effective forecasting. … Understand the impact of key retail events and promotions. … Put tools in place to effectively redistribute stock. Mục khác… • 26 thg 9, 2019
What is lost demand?
Lost Demanding a stock item is used when a customer requires an item that you do not have enough of or it is out of stock so they decide not to purchase the item from you.
How is cost of sales calculated?
To calculate the cost of sales, add your beginning inventory to the purchases made during the period and subtract that from your ending inventory. To calculate the total values of sales, multiply the average price per product or services sold by the number of products or services sold. 8 thg 3, 2021
What causes cost of sales to decrease?
There are many ways you can impact the cost of sales. We will enlist some of them down: Cash discount: If a company starts bulk buying their materials, it will affect the Cost of Goods Sold. When buying in larger quantities from the same supplier, the supplier will offer quantity based discounts and decrease the COGS.
Related searches
- How to be tall like NBA players
- what makes nba players so tall
- quora increase height
- Why basketball players are so tall
- Increase height basketball
- why nba players are so tall
- how to be tall like nba players
- tallest basketball player
- Does basketball make you taller
- why are basketball player usually tall
- are basketball players naturally tall
- why basketball players are so tall
- increase height basketball
- why are basketball players so skinny
- does basketball make you taller
- how are all basketball players so tall
- how tall should basketball players be
- Why NBA players are so tall
- how come basketball players are so tall
- how are basketball players so tall reddit
You have just come across an article on the topic how are basketball players so tall. If you found this article useful, please share it. Thank you very much.