What is the equation for coal gasification?
This process is a complex one that involves several steps. The first step is the gasification of coal, which involves the conversion of solid coal into a gaseous mixture. This is typically achieved by reacting coal with steam and oxygen at high temperatures.
The gasification process results in a mixture of gases, including hydrogen, carbon monoxide, carbon dioxide, methane, and nitrogen. This mixture is then cleaned and purified to produce a usable fuel gas.
The syngas, as it is known, can be used directly as a fuel or converted into other products, such as methanol or synthetic natural gas.
Coal gasification is a promising technology for producing clean and efficient energy from coal. It offers several advantages over traditional coal combustion, including:
Reduced greenhouse gas emissions: Coal gasification can be used to capture and store carbon dioxide, which is a major greenhouse gas.
Increased energy efficiency: Coal gasification can produce more energy from the same amount of coal than traditional combustion.
Flexibility: Coal gasification can be used to produce a variety of fuels and chemicals.
However, coal gasification is a complex and expensive process. It requires high temperatures and pressures, and it can produce a number of byproducts that need to be managed. Further research and development are needed to optimize the efficiency and cost-effectiveness of coal gasification technology.
What is the gasification method of coal?
Think of it as a controlled way to break down the coal molecules, releasing valuable gases like carbon monoxide, hydrogen, and methane. These gases are then cleaned and can be used as fuel for power generation, industrial processes, or even transportation.
Now, let’s compare this to traditional coal power plants. Those plants rely on burning coal, a process called combustion. In combustion, the coal burns completely, releasing heat that is used to generate steam and drive turbines.
Gasification is different. It’s like a gentler approach that unlocks the hidden potential of coal. By controlling the reaction, we can create a cleaner and more versatile energy source.
The syngas produced through gasification can be used in a variety of ways. For example, it can be used to generate electricity in gas turbines. The syngas can also be converted into liquid fuels, like methanol, which can be used in transportation.
Gasification offers a number of advantages over traditional coal combustion. It can produce cleaner emissions, generate electricity more efficiently, and reduce our reliance on fossil fuels.
What are the reactions related to coal gasification?
Pyrolysis occurs under all conditions of gasification. Tar is further broken down in a process called hydrocracking, producing methane (CH4), hydrogen (H2), and carbon monoxide (CO). Char undergoes hydrogasification and gasification reactions, also producing methane (CH4), hydrogen (H2), and carbon monoxide (CO).
Let’s dive a little deeper into these reactions:
Hydrocracking is a process that breaks down large hydrocarbon molecules (like those found in tar) into smaller molecules. This process is typically done in the presence of hydrogen, which helps to break the bonds between the carbon atoms. The hydrogen also reacts with the carbon to produce methane.
Hydrogasification is a similar process to hydrocracking, but it specifically refers to the reaction of hydrogen with char. This reaction produces methane, hydrogen, and carbon monoxide.
Gasification is a general term that refers to any process that converts a solid fuel into a gaseous fuel. In the context of coal gasification, it typically refers to the reaction of carbon (in the form of char) with oxygen and steam to produce carbon monoxide, hydrogen, and carbon dioxide.
The pyrolysis reaction is just the beginning of the process. The subsequent hydrocracking, hydrogasification, and gasification reactions are crucial for converting the coal into a usable gas fuel.
What is the reaction of gasification?
Let’s break down this process a little further. Imagine you have a piece of wood (our carbon source). When you heat this wood in the presence of steam and oxygen, it undergoes a chemical reaction. This reaction breaks down the wood into its individual components, releasing gases like hydrogen, carbon monoxide, and carbon dioxide. The resulting gas mixture is known as syngas, which is a valuable fuel source.
The specific gases produced during gasification depend on a few key factors, such as the temperature, pressure, and the type of carbon source used. For instance, if you use a high temperature and a high oxygen concentration, you’ll get a gas mixture with a higher proportion of hydrogen and carbon monoxide. These gases are valuable fuels for various applications, including power generation and chemical synthesis.
Essentially, gasification is a way to transform a solid fuel into a gaseous one. This gaseous fuel is more versatile and efficient, making it a valuable resource for various industrial processes.
What is the formula for coal gas?
While we can’t write a single formula for coal gas because it’s a mixture, these three components are the most abundant. However, it’s important to know that coal gas also contains other gases in smaller quantities, such as carbon dioxide (CO2), nitrogen (N2), ethane (C2H6), and benzene (C6H6). The exact composition of coal gas can vary depending on the type of coal used and the process conditions.
Coal gas was historically a major source of fuel and lighting, but its use has declined significantly due to the development of natural gas and other cleaner energy sources. The production of coal gas involves a complex series of chemical reactions. The process begins with heating coal to high temperatures in a sealed chamber called a retort. As the coal heats up, it undergoes a series of transformations, releasing various gases and leaving behind a solid residue called coke. The gases released from the retort are then collected and purified to produce coal gas.
It’s essential to remember that coal gas is a flammable mixture and should be handled with care. Due to its composition, it poses a risk of explosion if not properly contained and managed.
What is coal gasification conversion?
After the coal is cleaned up a bit, it goes into a special reactor. Inside the reactor, the coal hangs out with oxygen and steam. This creates a gas that can be burned for energy. If we use air as the oxygen source, we get a low-Btu gas. But, if we use pure oxygen, we get a medium- or high-Btu gas. The reason for this is that the nitrogen in air acts like a “spoiler” and makes the gas less powerful.
Think of it like this: Imagine you’re building a campfire. You can use regular air, which has nitrogen in it, to get a small, smoky fire. But, if you use a pure oxygen source, like a blowtorch, the fire is much bigger and hotter. That’s basically what happens with coal gasification, too!
Now, let’s dive a little deeper into the gasification process.
You know how we mentioned using oxygen and steam in the reactor? Well, these ingredients are crucial for turning coal into gas. The oxygen helps to burn the coal, and the steam reacts with the coal to produce hydrogen and carbon monoxide, which are the main components of the syngas. Syngas is a fancy name for the gas mixture that’s produced during gasification. It’s a very versatile fuel and can be used for various applications, like generating electricity, making synthetic fuels, or even producing chemicals.
The whole point of coal gasification is to transform the solid coal into a gaseous fuel that’s more efficient and cleaner than burning coal directly. This is because syngas can be burned more cleanly, producing fewer emissions. Plus, it can be used to make other things besides electricity, like liquid fuels.
So, the next time you hear about coal gasification, you’ll know it’s about turning coal into a more valuable, versatile fuel.
What is coal gasification by product?
If you’re using a non-slagging gasifier, you’ll get coarse bottom ash and fine fly ash.
Understanding Ash Byproducts
These byproducts are a significant part of the gasification process, so it’s essential to understand their characteristics:
Fly Ash: This is the finest ash, typically carried by the gas stream. It’s usually very fine, almost like a powder, and is often captured using filters.
Bottom Ash: This is the heavier ash that settles at the bottom of the gasifier. It’s typically coarser than fly ash and can be removed more easily.
Slag: This is a molten ash that forms at high temperatures, typically in high-temperature gasifiers. It’s typically removed as a liquid and can be further processed for different applications.
The type and amount of ash produced depend on the type of coal used, the gasification process, and the operating conditions.
The composition of the ash also varies depending on the coal source. The ash content can range from 5% to 20% of the coal’s mass, and it can contain a variety of elements like silica, alumina, iron oxide, and calcium oxide.
The ash byproducts can have various uses, such as:
Fly ash: Used in cement production, construction materials, and as a soil amendment.
Bottom ash: Used as a construction material and a soil amendment.
Slag: Used in the production of cement, road aggregate, and slag wool insulation.
It’s important to note that the management of these byproducts is crucial to ensure environmental sustainability. The ash needs to be disposed of or reused responsibly to prevent environmental damage.
What is the gasification of coal emissions?
Although it has environmental concerns, coal gasification offers a way to utilize coal resources for energy production. The syngas produced during gasification can be used in various ways. A major application is for power generation through combustion. Syngas can also be used as a feedstock for producing chemicals, fuels, and other valuable products.
Let’s explore the details of coal gasification and understand why it’s classified as a brown/black method:
The Process:
Coal gasification involves reacting coal with oxygen and steam at high temperatures and pressures. This process breaks down the coal’s complex structure, releasing syngas as a product. The exact composition of syngas depends on the type of coal used, the gasification conditions, and the specific technology employed.
Environmental Concerns:
Coal gasification, despite its potential, comes with environmental concerns. The process releases carbon dioxide, a greenhouse gas, contributing to climate change. Additionally, coal gasification can produce other pollutants, such as sulfur dioxide and nitrogen oxides, which can contribute to acid rain and air pollution.
The classification of coal gasification as brown/black highlights the significant environmental impact associated with it. This classification emphasizes the need for sustainable practices and technologies that minimize environmental harm while utilizing coal resources effectively. Ongoing research and development are exploring ways to improve the environmental performance of coal gasification, such as carbon capture and storage technologies, to reduce emissions and mitigate its environmental impact.
What is the chemical composition of coal gasification?
Coal gas is primarily made up of hydrogen, methane, and carbon monoxide. Let’s break down the typical composition:
Hydrogen makes up about 50% of coal gas.
Methane accounts for around 35%.
Carbon monoxide contributes about 10%.
It’s important to remember that these percentages are just approximations. The actual composition of coal gas can vary depending on the type of coal used and the conditions of the gasification process.
But, you might be thinking, “Why is this important?” Well, understanding the composition of coal gas is crucial because it impacts how we can use it. Hydrogen, for example, is a clean-burning fuel and is often used in fuel cells. Methane is also used as a fuel and can be used to generate electricity. Carbon monoxide, on the other hand, is a toxic gas, so it needs to be removed or processed before the coal gas can be used.
Let’s look a little closer at why these gases are so important in coal gasification.
Hydrogen is a powerful fuel source that burns cleanly without emitting harmful pollutants. It’s seen as a promising alternative to fossil fuels, and it plays a significant role in the move towards cleaner energy sources.
Methane, a primary component of natural gas, is another versatile fuel that can be used for electricity generation or directly in heating systems. It is often used as a building block for producing other chemicals.
Carbon monoxide, while toxic, has its own uses. It’s often used as a raw material in the production of other chemicals, such as methanol and acetic acid. In the context of coal gasification, however, the goal is to reduce or eliminate carbon monoxide before the coal gas can be used as a fuel.
Ultimately, coal gasification offers a way to utilize coal, a readily available resource, while minimizing its environmental impact. By understanding the chemical composition of coal gas, we can unlock its potential as a cleaner and more efficient energy source.
See more here: What Is The Gasification Method Of Coal? | Coal Gasification Can Be Represented By The Equation
What is coal gasification?
The main gases produced during coal gasification are carbon monoxide, hydrogen, methane, and carbon dioxide. These gases can be used for various purposes, including:
Generating electricity: The gas mixture can be burned to produce heat, which can then be used to generate electricity in a power plant.
Producing synthetic fuels: These gases can be further processed to create synthetic fuels like methanol and dimethyl ether, which can be used as alternatives to traditional fuels.
Creating chemicals: The gases produced from coal gasification can be used as raw materials for the production of other chemicals like ammonia and fertilizers.
The process of coal gasification involves several steps, each crucial to the overall transformation of coal into gas. Here’s a simplified explanation:
1. Coal Preparation: The coal is first crushed and dried to ensure a consistent and uniform feedstock.
2. Gasification: The prepared coal is then fed into a gasifier, where it reacts with oxygen and steam at high temperatures. This process generates a syngas (synthesis gas) consisting primarily of carbon monoxide, hydrogen, and methane.
3. Gas Cleaning: The syngas produced is often contaminated with impurities such as dust, tar, and sulfur. These impurities are removed through various cleaning processes to ensure the gas is suitable for its intended use.
4. Further Processing: Depending on the intended application, the cleaned syngas can be further processed. For instance, it can be converted to methanol or dimethyl ether by adding catalysts.
Coal gasification offers a potential alternative to traditional fossil fuel sources. While it does have environmental concerns, ongoing research and advancements in technology are continuously improving the efficiency and sustainability of this process.
How do you calculate a gasification process?
* C + O2 = CO2 with delta H = -94.05 kcal/mol
This equation represents the combustion of carbon with oxygen to produce carbon dioxide. The delta H value of -94.05 kcal/mol indicates that this reaction releases heat, making it exothermic.
* H2 + 0.5O2 = H2O with delta H = – 68.3 kcal/mol
This equation represents the combustion of hydrogen with oxygen to produce water. Similar to the previous reaction, the delta H value of -68.3 kcal/mol signifies that this reaction also releases heat, making it exothermic.
These exothermic reactions provide the necessary heat to drive the endothermic reactions within the gasifier. This process efficiently converts solid fuels like biomass or coal into a combustible gas mixture that can be used for power generation or other industrial applications.
Now, let’s delve deeper into the calculations behind gasification. The overall efficiency of the gasification process hinges on the equilibrium between these competing reactions. The key to understanding how to calculate this process lies in the concept of Gibbs Free Energy.
Gibbs Free Energy (ΔG) is a thermodynamic property that helps determine the spontaneity of a reaction under constant temperature and pressure. It’s calculated using the following equation:
ΔG = ΔH – TΔS
where:
ΔG is the Gibbs Free Energy change
ΔH is the enthalpy change (heat released or absorbed)
T is the absolute temperature
ΔS is the entropy change (measure of disorder)
To determine the equilibrium of a gasification reaction, we analyze the Gibbs Free Energy change for each reaction involved. A negative ΔG value indicates a spontaneous reaction, while a positive ΔG value indicates a non-spontaneous reaction.
The gasification process involves a complex interplay of these thermodynamic principles. To calculate the overall efficiency and predict the output of a gasification process, we need to consider factors like:
Type of fuel: Different fuels have varying compositions and reactivity, impacting the reactions and the overall efficiency.
Operating temperature: The temperature inside the gasifier significantly influences the rate of reactions and the equilibrium between the various products.
Oxygen supply: The amount of oxygen available determines the extent of combustion reactions, affecting the heat generated and the gas composition.
Pressure: The pressure inside the gasifier influences the equilibrium of the reactions and the composition of the syngas produced.
By carefully analyzing the thermodynamic parameters and considering the specific conditions of the gasifier, we can calculate the expected outputs and optimize the process for maximum efficiency. The intricate calculations and understanding of the underlying principles are crucial for harnessing the power of gasification technology.
What is the Order of non-catalytic gasification reactivities of Cokes?
Here’s the order we found:
1. French bituminous coal
2. Pingshuo gas coal inertinite
3. Pingshuo gas coal vitrinite
4. Pingshuo gas coal
5. Fuxin long-flame coal
6. Fengfeng meager coal
7. Dongshan lean coal
This means that French bituminous coal has the highest non-catalytic gasification reactivity, while Dongshan lean coal has the lowest.
Let’s dive a little deeper into why this happens.
The non-catalytic gasification reactivity of a coke is primarily influenced by its physical and chemical properties, including:
* Porosity: Coals with higher porosity have more surface area available for reaction with the gasifying agent. This leads to a faster gasification rate.
* Ash content: Ash can either promote or hinder gasification depending on its composition. High ash content can block pores and hinder gasification, while certain ash components can act as catalysts and promote gasification.
* Carbon structure: The arrangement of carbon atoms in the coke’s structure can affect its reactivity. Coals with a more disordered carbon structure tend to be more reactive.
The order of reactivities we observed is likely due to variations in these properties across the different coal types. For instance, French bituminous coal, which shows the highest reactivity, might have a high porosity and a favorable carbon structure. On the other hand, Dongshan lean coal, with the lowest reactivity, might have lower porosity, a more ordered carbon structure, or an ash composition that inhibits gasification.
It’s important to note that these are just general trends, and the specific reactivity of a coke can be influenced by other factors such as particle size, temperature, and the type of gasifying agent used. However, understanding these general trends can help us predict the gasification behavior of different cokes and optimize gasification processes.
What is integrated coal gasification combined cycle?
During gasification, coal is partially oxidized with air, oxygen, steam, or carbon dioxide under controlled conditions. This process produces a mixture of gases, primarily carbon monoxide (CO) and hydrogen (H2), which are the key components of syngas. Syngas is then cleaned to remove impurities like sulfur and particulate matter before being used to power a gas turbine. The hot exhaust gases from the turbine are used to generate steam, which drives a steam turbine to produce additional electricity.
This combination of gas and steam turbines in a single power plant is what makes IGCC a combined cycle system. It allows for higher efficiency and lower emissions compared to traditional coal-fired power plants.
Let’s break down the process step by step:
1. Coal Preparation: Coal is crushed and pulverized to a fine powder to increase its surface area and improve gasification efficiency.
2. Gasification: The pulverized coal is fed into a gasifier, where it reacts with the chosen gasifying agent (air, oxygen, steam, or carbon dioxide). This process converts the coal into syngas, a mixture of combustible gases, primarily CO and H2.
3. Syngas Cleaning: The syngas produced during gasification contains impurities like sulfur, particulate matter, and other undesirable compounds. These impurities need to be removed to ensure efficient and clean combustion.
4. Combustion and Power Generation: The cleaned syngas is then combusted in a gas turbine to generate power. The hot exhaust gases from the gas turbine are then used to generate steam in a heat recovery steam generator (HRSG). The steam drives a steam turbine, producing additional electricity.
5. Combined Cycle Efficiency: The combination of the gas and steam turbines results in a significantly higher efficiency compared to traditional coal-fired power plants, where only steam turbines are used. This is because the IGCC system utilizes the heat from the gas turbine exhaust to generate additional power.
IGCC is a promising technology for clean coal power generation. It offers several advantages over traditional coal-fired power plants, including:
Lower emissions: IGCC plants can achieve significantly lower emissions of sulfur dioxide (SO2), nitrogen oxides (NOx), and particulate matter compared to traditional coal-fired power plants. This is due to the gasification process, which removes many impurities from the coal before combustion.
Higher efficiency: The combined cycle system in IGCC plants allows for higher energy conversion efficiency, resulting in more electricity generated per unit of coal used.
Carbon capture potential: IGCC plants are well-suited for carbon capture and storage (CCS) technologies. The syngas produced during gasification can be treated to remove CO2, which can then be captured and stored underground.
IGCC technology is still under development, but it has the potential to play a significant role in reducing greenhouse gas emissions and providing a cleaner source of energy from coal.
See more new information: countrymusicstop.com
Coal Gasification: The Equation Explained
Coal gasification is a process that transforms coal, a solid fossil fuel, into a mixture of gases, primarily syngas. This process is often represented by a simple chemical equation, but the reality is much more complex. Today, we’ll dive into the intricacies of coal gasification and understand the chemical equation that serves as a starting point for this fascinating technology.
The Simplified Equation
Let’s start with the basic representation of coal gasification:
Coal + Steam + Oxygen → Syngas
This equation is a good starting point, but it doesn’t fully capture the complexities involved. We need to understand what syngas is and the chemical reactions that actually occur.
Syngas: The Heart of Coal Gasification
Syngas, or synthesis gas, is a mixture of primarily carbon monoxide (CO) and hydrogen (H2). It can also contain other gases like carbon dioxide (CO2) and methane (CH4), depending on the specific gasification process and coal type.
A Deeper Look: The Chemical Reactions
The transformation of coal into syngas involves a series of complex chemical reactions. Let’s break down the main steps involved in the coal gasification process:
1. Drying: The first step involves drying the coal to remove any moisture. This is crucial because moisture can interfere with the gasification process.
2. Pyrolysis: In this stage, the coal is heated in the absence of oxygen. This process breaks down the coal into volatile gases and char.
3. Gasification: This is the core of the process. The char from pyrolysis reacts with steam and oxygen in a gasifier. The primary reactions in this stage are:
Water-gas shift reaction:
CO + H2O → CO2 + H2
This reaction produces hydrogen and carbon dioxide.
Boudouard reaction:
C + CO2 → 2CO
This reaction produces carbon monoxide.
4. Cleanup: The gas produced from the gasifier contains impurities like sulfur compounds, tar, and dust. These impurities need to be removed before the syngas can be used.
Different Gasification Technologies
There are various gasification technologies, each with its unique characteristics and suitability for different coal types and applications. Some of the commonly used gasification technologies include:
Fixed-bed gasification: This technology involves feeding coal from the top of a reactor, where it moves downwards in a fixed bed.
Fluidized bed gasification: This method uses a bed of inert particles to carry the coal through the reactor. The coal is fluidized, meaning it behaves like a liquid, allowing for better mixing and heat transfer.
Entrained flow gasification: This technology involves injecting coal particles and oxygen into a high-velocity stream of gas. The high temperatures and rapid mixing promote fast and efficient gasification.
Applications of Coal Gasification
Coal gasification has many applications, including:
Power generation: Syngas can be used to generate electricity in power plants, providing an alternative to traditional coal-fired power plants.
Production of fuels: Syngas can be converted into various fuels, including synthetic natural gas, diesel fuel, and methanol.
Chemical production: Syngas is a valuable feedstock for the chemical industry, used to produce ammonia, fertilizers, and other chemicals.
Hydrogen production: Syngas can be used to produce hydrogen for various applications, including transportation and fuel cells.
Advantages of Coal Gasification
Coal gasification offers several advantages over traditional coal combustion:
Higher efficiency: The gasification process can be more efficient than direct combustion, with the potential to capture and utilize the energy released.
Reduced emissions: Coal gasification can lead to lower emissions of sulfur dioxide, nitrogen oxides, and particulate matter.
Flexibility: Syngas can be used in various applications, making it a versatile energy source.
Utilization of low-grade coal: Coal gasification can utilize lower-grade coal that is not suitable for direct combustion.
Challenges and Future Directions
Despite its advantages, coal gasification faces several challenges:
High capital cost: The technology requires substantial investment, making it less attractive for some applications.
Complex and demanding process: Coal gasification is a complex and demanding process that requires specialized equipment and expertise.
CO2 capture and storage: CO2 capture and storage are crucial for achieving significant emissions reductions from coal gasification.
Research and development efforts are ongoing to address these challenges and improve the efficiency and sustainability of coal gasification technology. These efforts include:
Improving gasifier design: Research focuses on developing more efficient and cost-effective gasifier designs.
Developing more efficient and affordable CO2 capture technologies.
Exploring new applications for syngas and its products.
Conclusion
Coal gasification is a promising technology with the potential to address several environmental and energy challenges. While it’s not a perfect solution, continuous research and development are paving the way for cleaner and more efficient coal-based energy systems.
FAQs About Coal Gasification
1. Is coal gasification a clean technology?
Coal gasification offers potential for cleaner energy production than traditional coal combustion. It can reduce emissions of pollutants like sulfur dioxide and particulate matter. However, it is crucial to capture and store CO2 to achieve significant emissions reductions.
2. What are the main products of coal gasification?
The main products of coal gasification are carbon monoxide (CO) and hydrogen (H2), collectively known as syngas. The specific composition of syngas can vary depending on the gasification process and coal type.
3. What is the difference between coal gasification and coal combustion?
Coal combustion directly burns coal with oxygen to release heat energy. In coal gasification, coal reacts with steam and oxygen to produce a mixture of gases, primarily syngas.
4. Why is coal gasification important?
Coal gasification offers a way to utilize coal resources more efficiently and with potentially lower emissions than direct combustion. It can be used to produce electricity, fuels, chemicals, and hydrogen.
5. What are the environmental impacts of coal gasification?
The environmental impacts of coal gasification depend on the specific process and how emissions are managed. While it can reduce some pollutants, CO2 emissions are a major concern. Carbon capture and storage technologies are crucial to minimize the environmental impact.
6. What are the future prospects of coal gasification?
Coal gasification is a promising technology with potential for cleaner and more efficient energy production. However, challenges related to cost, complexity, and CO2 capture need to be addressed. Ongoing research and development are focusing on improving efficiency and sustainability.
7. Is coal gasification a viable alternative to renewable energy sources?
Coal gasification can play a role in transitioning to a low-carbon future, but it is not a direct replacement for renewable energy sources. It is essential to diversify energy sources and invest heavily in renewable energy technologies to achieve sustainability goals.
Coal Gasification – an overview | ScienceDirect Topics
Gasification of coal is a process in which coal is partially oxidated by air, oxygen, steam or carbon dioxide under controlled conditions to produce a fuel gas. The hot fuel gas is ScienceDirect
Solved Coal gasification can be represented by the | Chegg.com
Coal gasification can be represented by the equation: 2 C (s) + 2 H2O (g) ? CH4 (g) + CO2 (g) ?H = ? Use the following information to find ?H for the reaction above. C (s) + H2O Chegg
Solved Coal gasification can be represented by the equation
Question: Coal gasification can be represented by the equation: 2 C(s) + 2 H2O(g) → CH4(9) + CO2(g) AH = ? Use the following information to find AH for the reaction above. Chegg
Coal Gasification | SpringerLink
Coal gasification is an important industrial process for converting raw coal into more useful and cleaner carbon feedstocks for use in power generation and as Springer
Gasification of coal – IspatGuru
The major gasification reactions which take place are (i) water gas shift reaction, (ii) Boudouard reaction, (iii) shift conversion, and (iv) methanation. In water gas shift reaction where the partial oxidation IspatGuru
Solved Coal gasification can be represented by the equation
Science. Chemistry questions and answers. Coal gasification can be represented by the equation: 2 C (s) + 2 H2O (g) – CH4 (g) + CO2 (g) AH = ? Use the following information Chegg
Coal gasification can be represented by the equation: 2C(s)
The production of syngas from carbon and water and air is known as the coal gasification. The syngas is mixture of some gases, that are carbon monoxide (CO), natural gas: Homework.Study.com
Coal Gasification
Coal Gasification
C.2 Coal Gasification And Liquefaction (Sl)
Coal Gasification Simulation Using Factsage 7.2
Gasification Animation
Link to this article: coal gasification can be represented by the equation.
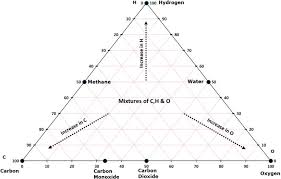
See more articles in the same category here: blog https://countrymusicstop.com/wiki